Dewaxed Casting Production Process
OEM is entrusted to manufacture stainless steel, carbon steel and other alloy steel products by dewaxing casting.
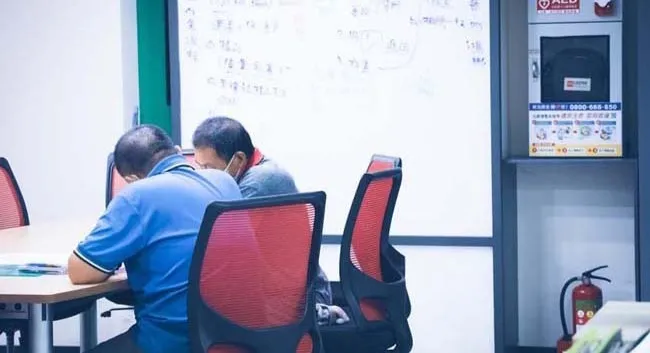
Step.01 Business Discussion and R&D of Specimens

Step.02 Preparation of Wax Fittings
The client will provide molds or the drawings of specimens to have the mold factory manufacture the molds. After the mold enters the factory, we inspect the condition of the mold and wax parts before starting the wax injection process. Then, wax repair and burr removal will be carried out to confirm the smooth and complete appearance of the product, and a string tree will be assembled according to the appropriate product scheme.
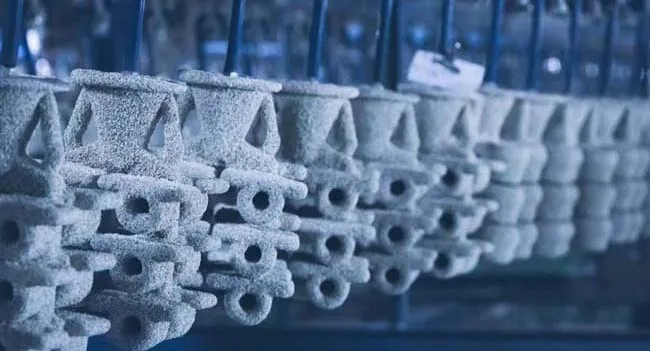
Step.03 Shell Mold Operation
Washing and Dipping/Sand Leaching/Drying/Dewaxing
The string tree made of wax pieces is repeatedly dipped and sand leached, and the product is covered with refractory material layer by layer. Each layer of refractory material must wait until it has dried before the next layer can be added. The temperature and humidity in this process have to be strictly controlled.
After the solid refractory material is completed, it is placed in a high-temperature furnace, enabling the wax to melt and flow out to form the required shell mold.
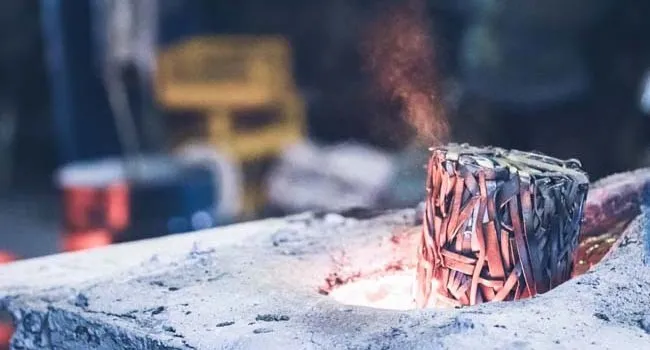
Step.04 Smelting
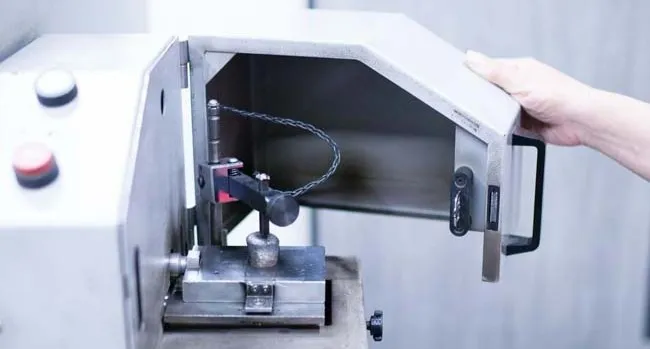
Step.05 Material Testing
After smelting, the material is first analyzed with a spectrometer to confirm that the material composition meets the customer requirements and international standards.
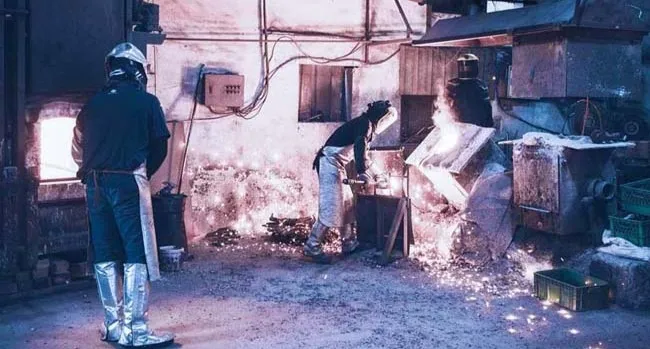
Step.06 Smelting and Casting
After dewaxing, the shell mold is put into a sintering furnace to increase the strength of the shell mold. After confirming that the inside of the shell mold is clean and complete, and when the expected time and temperature have been reached, we proceed with casting.
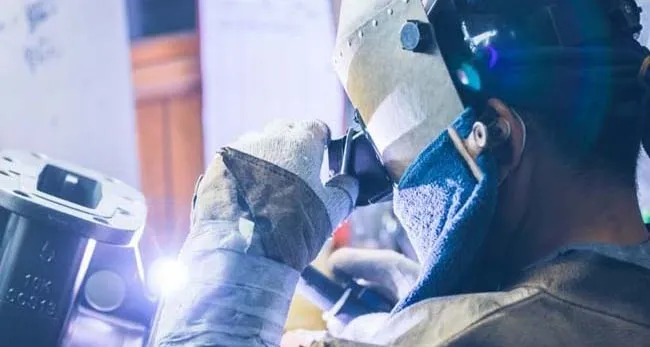
Step.07 Post-Treatment
After the shell mold has cooled, it is moved to a shell shaker, and the refractory shell mold is peeled off for post-treatment; this way the product has a clean and even appearance.
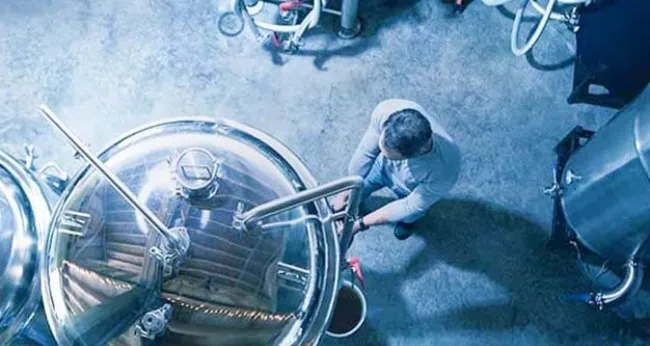
Step.08 Heat Treatment
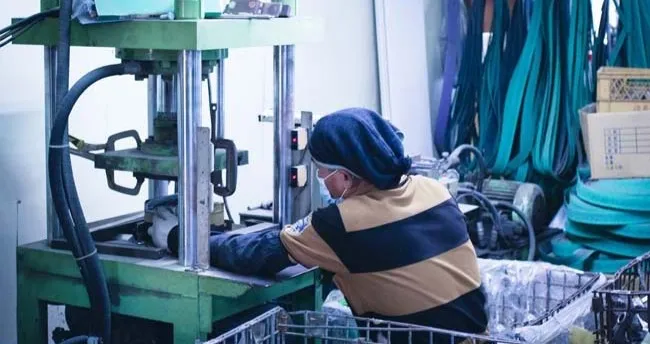
Step.09 Shaping
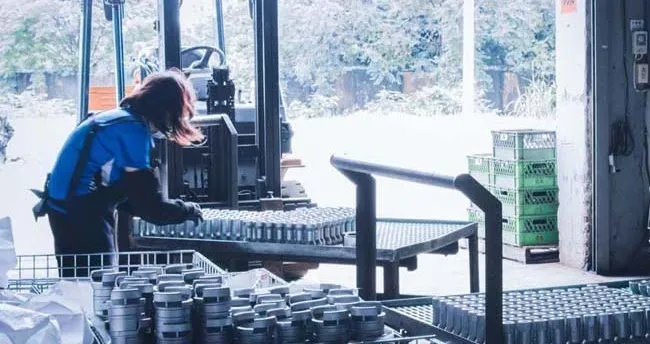
Step.10 Inspect Products and Shipments
(e.g., material certificate, hardness certificate) according to the customer's requirements, and deliver it to the customer's designated place.